WJA Member Spotlight – Flowplant Group
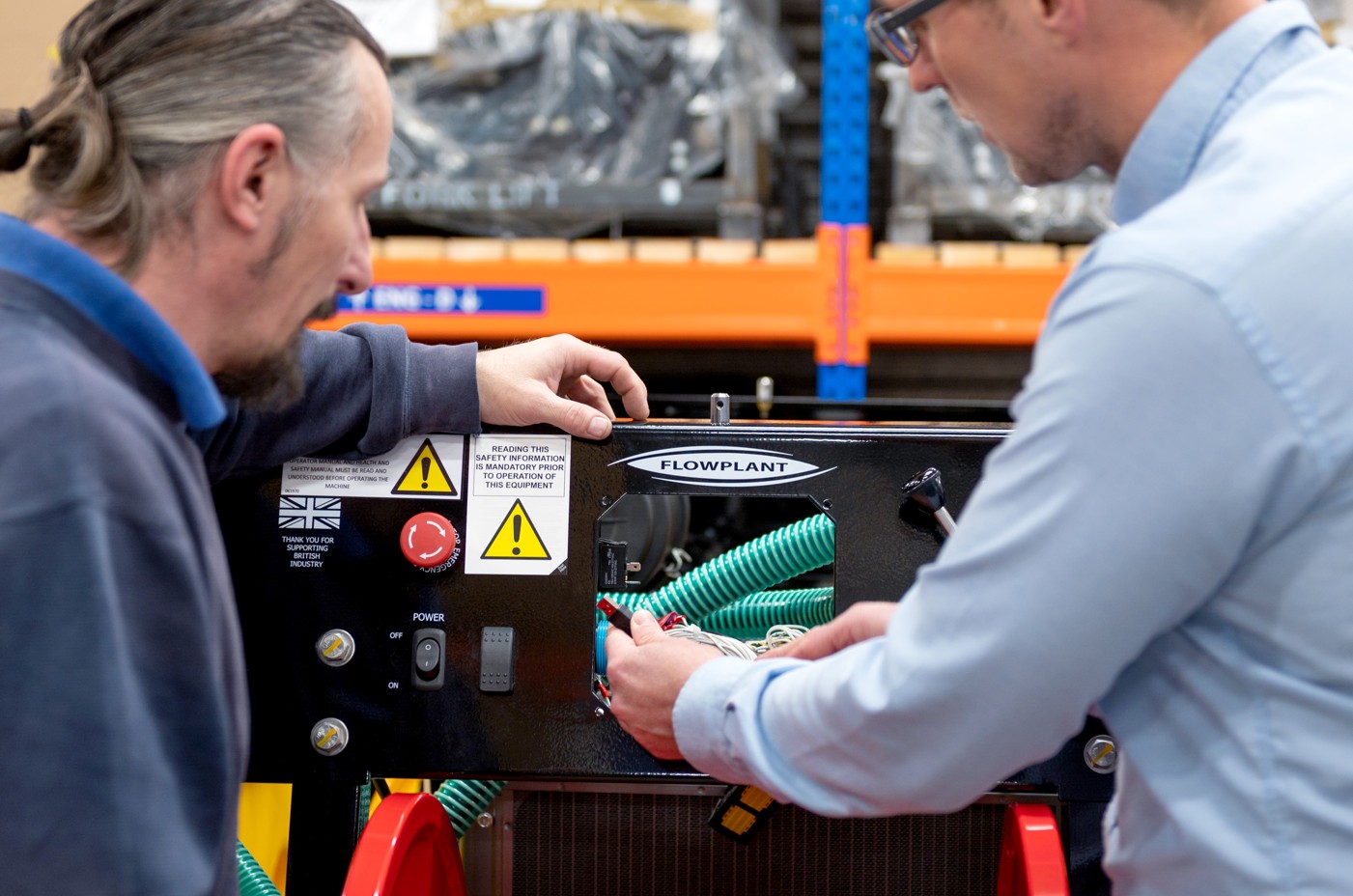
Company name: Flowplant Group Ltd
Company representative: Steve Smith
Job title: Group Managing Director
What services do you deliver to the water jetting industry?
Flowplant specialises in the production of high and ultra-high-pressure pumps and systems. Our range includes units for hydroblasting, flushing, duct desilting, and tube and pipe cleaning.
We take pride in engineering bespoke solutions that meet global standards, including those set by the Water Jetting Association.
Just as importantly, we have a team of engineers who maintain our equipment for customers, so it remains reliable and effective across diverse industries.
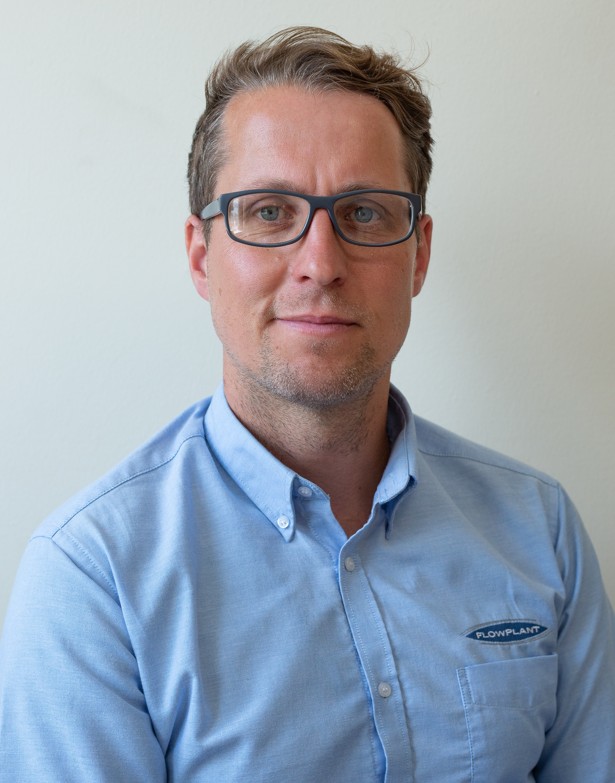
What are the three most important elements of service delivery for your customers and why?
Firstly, one of our distinctive features is the in-house manufacturing of the Harben radial diaphragm pump. This pump has advantages for many industries, including an ability to run dry, chemical compatibility, and the capacity to function with subpar fluids, containing small solid particles.
Secondly, we’re a bespoke engineering company, capable of crafting solutions tailored to precise customer requirements. Our flexible design approach accommodates last-minute changes, so our products align with the evolving needs of our clients.
Thirdly, we remain pioneers in the high-pressure sector. This gives us the engineering experience and expertise we need fabricate high-quality equipment and consistently deliver high quality solutions.
What have been the business highlights for Flowplant Group Ltd over the last 12 months?
We’ve maintained our success in the telecoms industry with a unique desilting solution. We supply the only equipment capable of effectively clearing cable ducts that are over 500 metres long. This capability sets us apart and has allowed us to maintain our leading position in this sector over the last 12 months.
Tell us something that you think anyone outside the industry will find amazing about your products and/or services.
Amidst certain awe-inspiring aspects shrouded by non-disclosure agreements, there’s one thing we can loudly proclaim – the unmatched reliability of the Harben pump.
We’re consistently servicing pumps that have been in operation for an astounding 30-40 years. This enduring performance speaks volumes about the quality and longevity of our products, and it’s a key reason why customers worldwide return to us time and again.
What’s the biggest change in technology or process you have witnessed in your service sector in recent years?
The continued advances in software engineering enables our products to be controlled in a much more detailed way. New hardware also allows us to measure and control processes in ways we have been unable to in the past. I’ve grown from a mechanical background, but I have a love for the electrical world.
The use of electrical and digital devices also ensures we can control the units to such levels where safety is increased. Surely this, along with new and improved PPE, are the best enhancements in the water jetting sector. Keeping the user safe should be everyone’s priority.
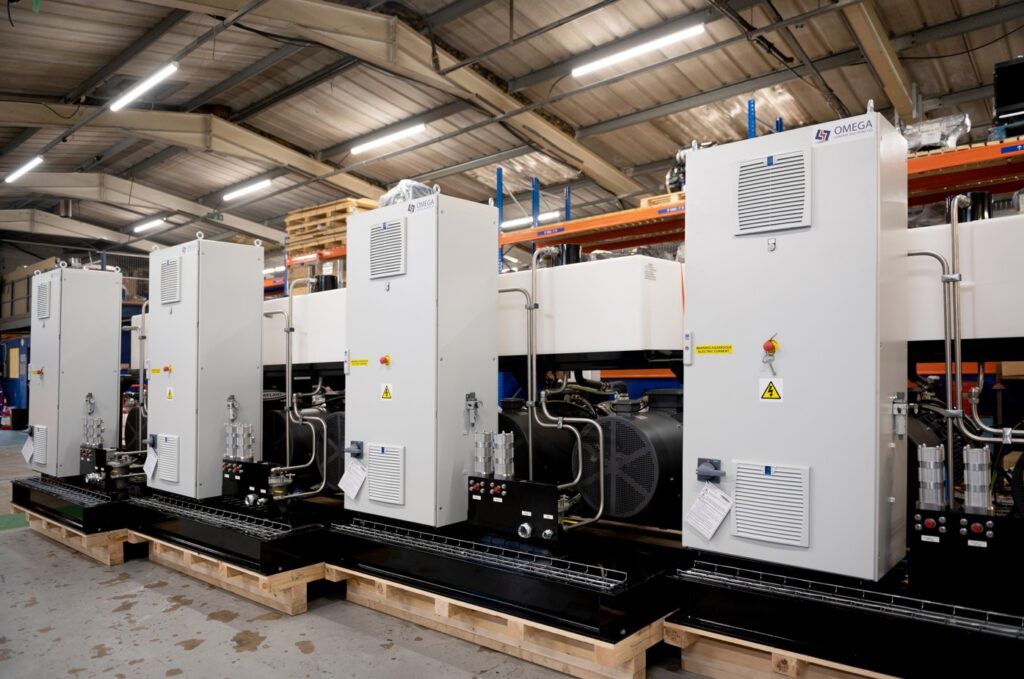
What do you think will be the biggest changes or challenges over the next 10 years?
Undoubtedly, our focus lies on sustainability and minimising reliance on fossil fuels. The demand for pumping fluids at such high flows and pressures involves substantial energy consumption, a critical concern in reducing carbon footprints.
While we currently adhere to legal requirements for engines and motors, our future efforts involve exploring the potentials of electric and hydrogen-powered units to align with our environmental goals.
What are you most proud of about the way your team supports your customers?
Flowplant’s foundations are built on four unwavering core values that guide our every action:
- Customer focused.
- Accountable.
- Fun and respect.
- e deliver on promises.
We work continuously to deeply embed these values in our culture, to empower and teams and set clear standards for new members. They guide every action, so we meet delivery deadlines, exceeding customer expectations, and fostering exceptional experiences for all our valued clients.
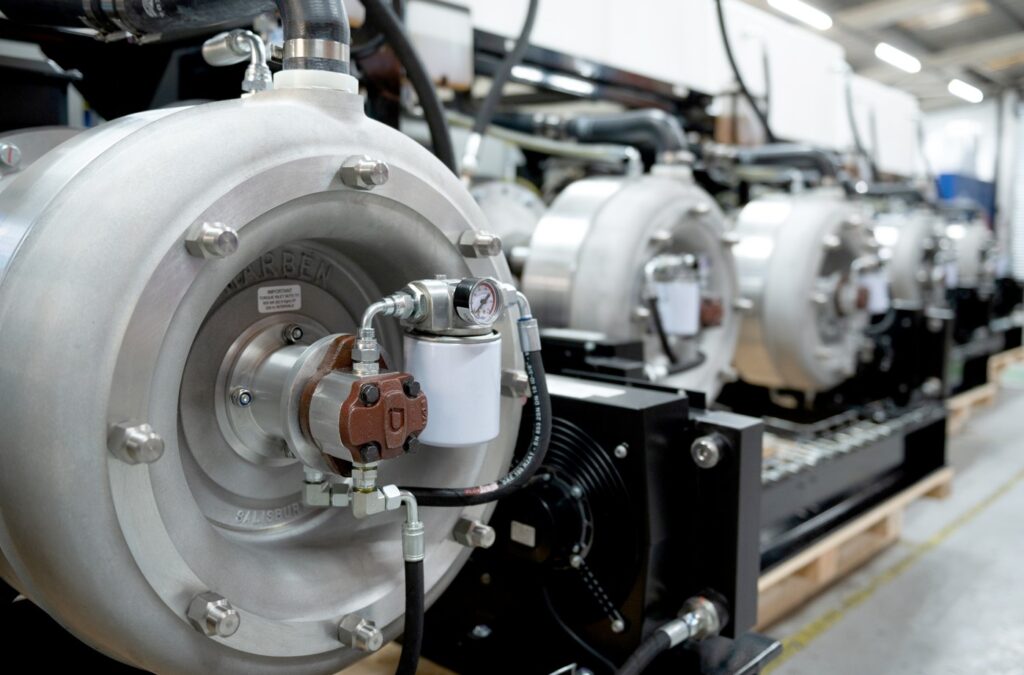
Why did Flowplant decide to join the WJA?
Flowplant’s affiliation with the WJA significantly predates my tenure, but our steadfast membership has been a source of immense pride to me.
Our commitment to the association’s codes of practice underpins our production of equipment that maximises safety within the industry. The WJA is a globally-recognised association. Our participation with it brings us daily advantages that continually enhance our operations.
We’ve also been offering comprehensive WJA training for quite some time now, facilitated by our three exceptional direct trainers. It’s another way we can contribute to enhanced safety and quality in the water jetting industry.
You are personally involved in the WJA. Explain your role and why you participate.
I sit on both the WJA’s technical committee and its ruling council. This enables me to contribute directly to the association’s development and to enhancing safety across the water jetting industry.
I work with a diverse and extremely experienced group of water jetting professionals on these committees. This enables us to create and develop very robust and high-quality codes of practice that are recognised increasingly around the world.
Being relatively new to the industry (11 years), my involvement has been a great learning experience, thanks to the expertise and insights of other committee members.
Collaboration within the committees is essential for problem-solving, as different perspectives offer insights into various situations. This collective knowledge exchange is particularly valuable in addressing emerging challenges.
What do you think are the WJA’s biggest achievements?
The industry’s safety has notably improved with the implementation of the code of practices, and the ongoing marketing efforts are equally commendable. Encouraging more companies to join this association is vital, as it collectively contributes to enhancing safety standards in this inherently hazardous sector.
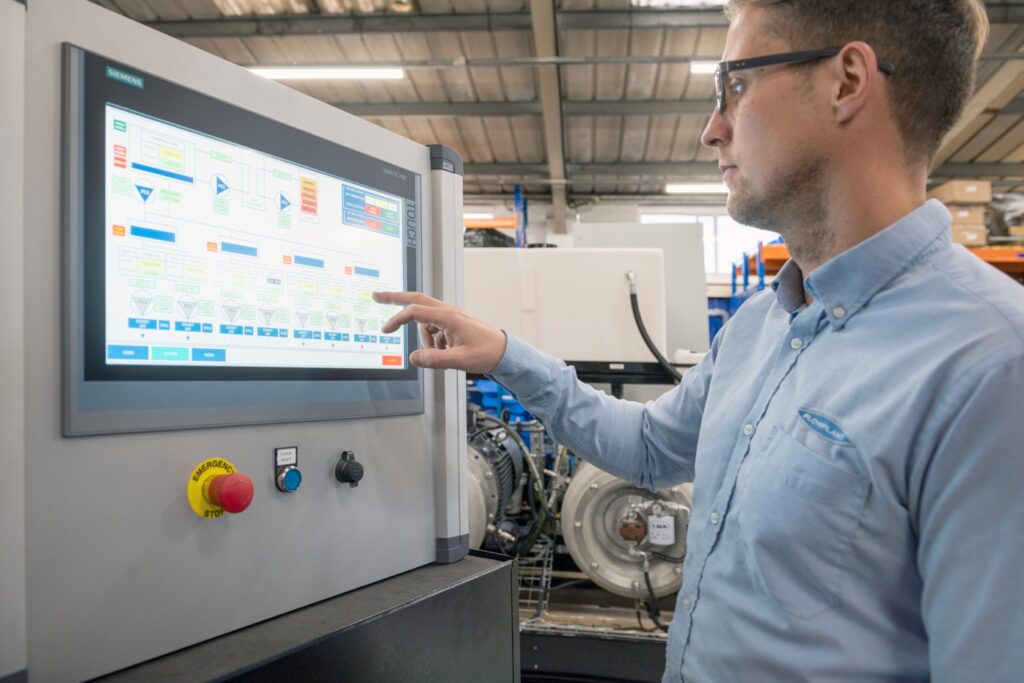
If Flowplant Group Ltd was an animal, what kind would it be?
A chameleon.
Just as a chameleon gains an edge through continuous transformation, Flowplant continuously engineers unique solutions to suit the specific needs of each customer across many different industries.
Do you want to be part of the WJA too?
Would your business or organisation benefit from being a WJA member?
Find out more about membership categories and the advantages of joining a body that represents the UK water jetting industry. There is a category for international members as well. Telephone: +44 (0) 20 8320 1090. Email: info@waterjetting.org.uk