WJA Member Spotlight – Abdex
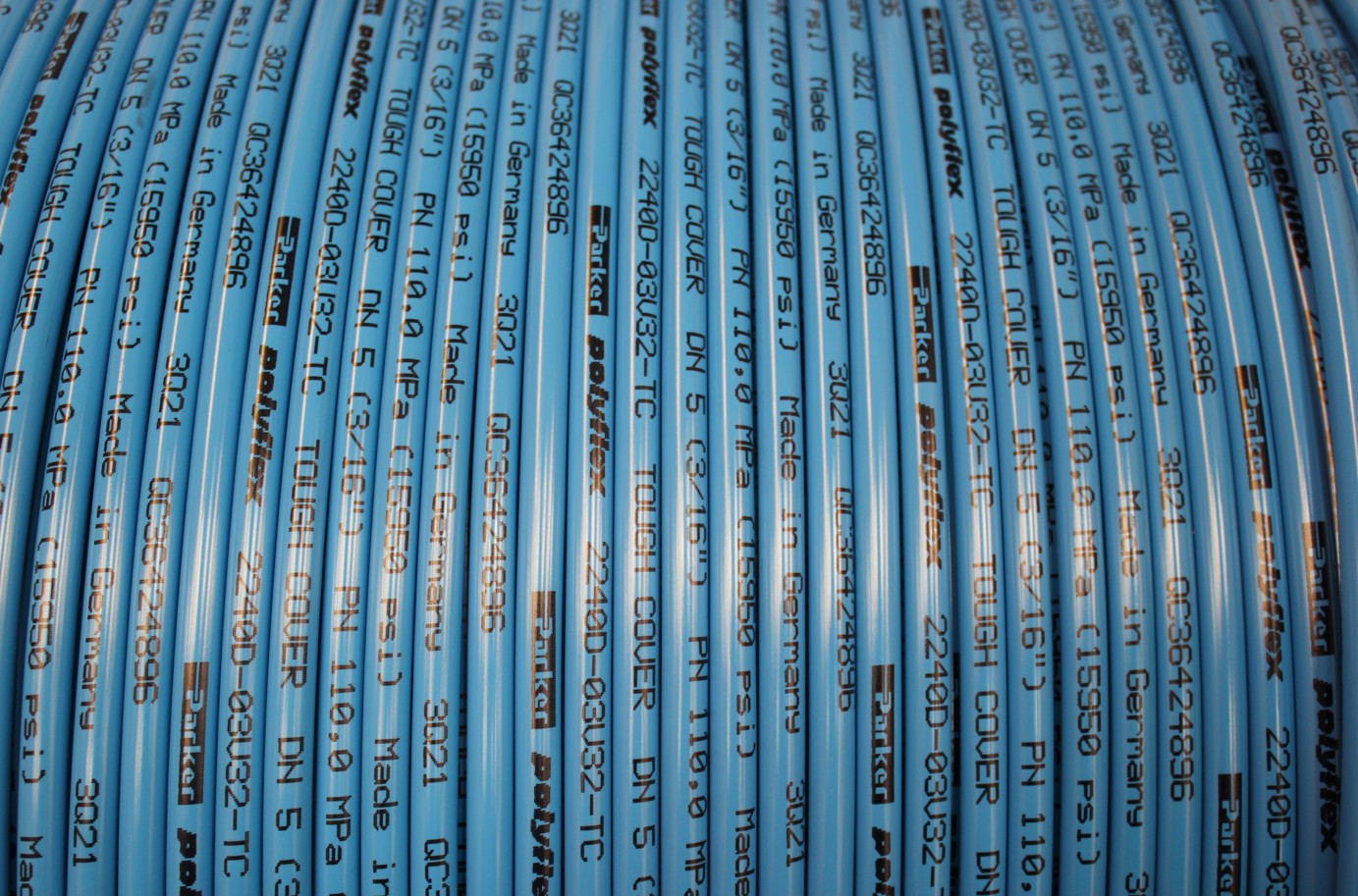
Company name: Abdex
Company representative: Stefan Gunter
Job title: Sales Director

What services do you deliver to the water jetting industry?
Abdex supplies sewer jetting hose, water blast hose, high pressure and UHP hose assemblies up to 4000 bar working pressure.
What are the three most important elements of service delivery for your customers and why?
Fast/Flexible delivery – The customer is our life blood and will always work tirelessly to ensure we give the best possible service.
Assembly/Testing – The customer can be confident that they are buying the best quality and tested hose assemblies, which are fully supported by Abdex/Parker with a global warranty.
Making it as easy to find technical data and place an order – The customer can be confident that we will provide the best technical data and support when quoting. I think we make it easy for the customer, of course we can improve but we are always ready to do business.
What have been the business highlights for Abdex over the last 12 months?
Growth during the Covid pandemic has been fantastic. Stability of our business in an unstable world has shown our strength as a business to support our customers.
Tell us something that you think anyone outside the industry will find amazing about your products
When the firing pin in a firearm strikes the primer, it ignites the charge inside the case, creating an explosion that generates a huge amount of pressure, often exceeding 50,000 PSI (344.7 MPa).
Abdex Parker Polyflex hoses have working pressures up 58,000PSI (400 Mpa) and to guarantee safety they are tested above 70,000PSI (482 Mpa).
What’s the biggest change in technology or process you have witnessed in your service sector in recent years?
It isn’t really “technology” but slowly I see people treating hoses as an asset and not an afterthought (compared with the rest of the hydraulic system – such as the jetting machines).
The hoses are not expensive compared to the capital equipment, however the hoses are a critical part to any system and should be treated with respect.
In regards to testing, the data logging technology has advanced to give our customers live data (via our Abdex asset management A-test APP) the minute their assembly comes off our test rig.
The cloud based technology allows the customer and Abdex to asset manage the hose for its lifetime in regards to identification, inspections, re-testing and replacement. In short the technology should increase the lifetime of the hose and most importantly makes the hose market safer.

What do you think will be the biggest changes or challenges over the next 10 years?
Attracting young talent into our industry.
What are you most proud of about the way your team supports your customers?
The way we consistently respond to customer requirements. Nothing is ever too much and we are always flexible to ensure a quality product goes out of the door time and time again.
How long has Abdex been a member of the WJA?
10 years
Why did the company decide to join?
So we can fully understand the applications and customer requirements.
You are personally involved in the WJA. Explain your role and why you participate.
I sit on the technical committee which enables me to update the WJA with the latest regulations in regards to hose testing and supply.
What do you think are the WJA’s biggest achievements?
The WJA’s commitment to improving safety has been its main priority and the biggest influence on the water jetting industry. That’s reflected in the number of training courses delivered to market, and importance within the industry of the WJA’s blue and red codes of practice.
If Abdex was an animal, what kind would it be?
A leopard – The ultra-high pressures our hoses allow represent the speed and power and I would like to think that we have the agility. They say a leopard does not change its spots. Our core product values do stay the same, but I also know that we change direction as required.
