Water Jetter Steven is Proud to Share the WJA’s Anniversary
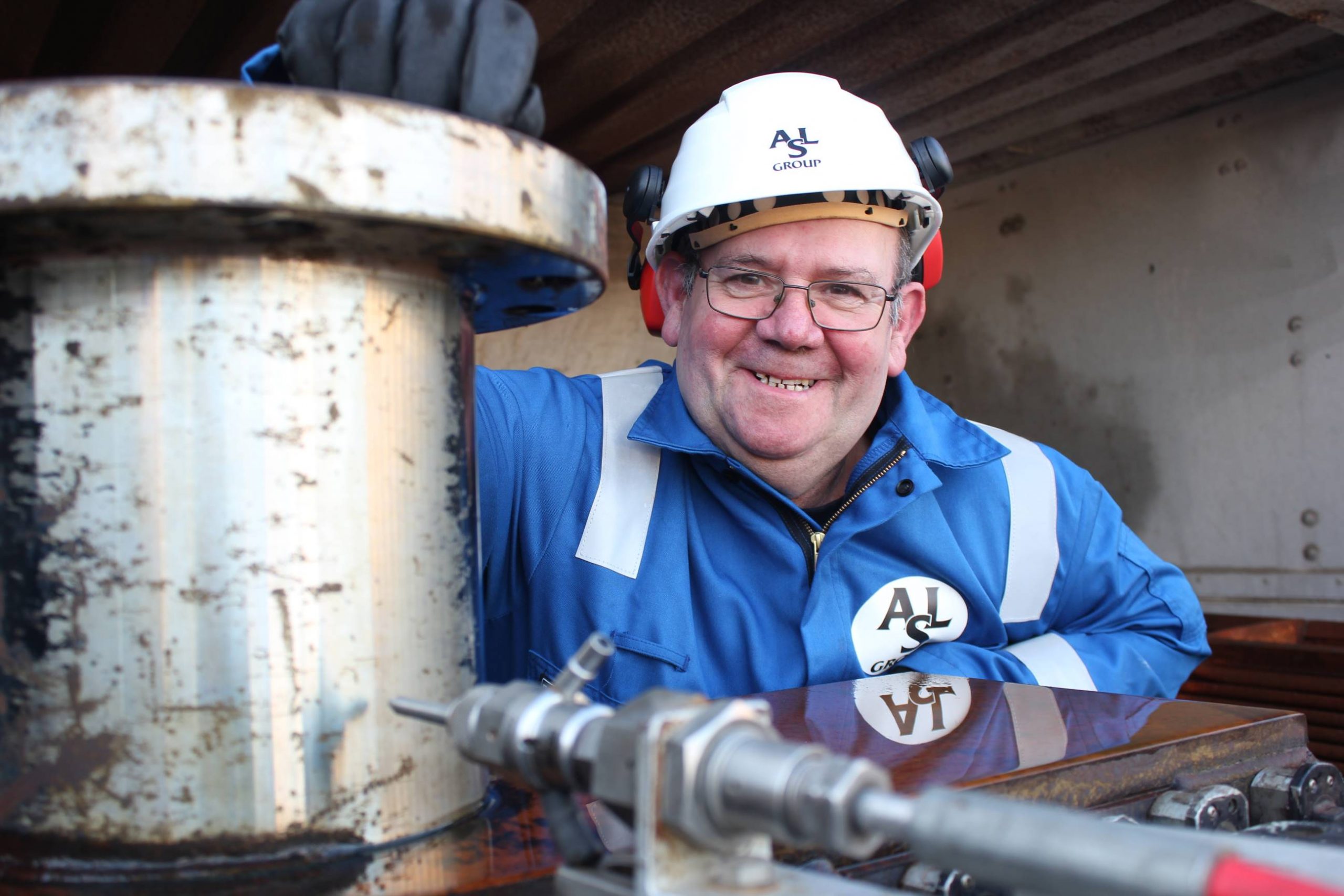
Steven Sargent had just been made redundant so had nothing to lose by going into the offices of one of the pioneers of water jetting to ask if they had any jobs.
It turned out he had everything to gain, because that spur of the moment decision has led to a 40-year career as a water jetter – and a skilled job he still loves today.
Steven, aged 64, started working for Walton Mole Company on Teesside in 1980, the same year that the Water Jetting Association (WJA) was founded.
That puts him in a good position to comment on the changes in the UK water jetting industry as the WJA celebrates its 40th anniversary – and those changes have been profound.
Steven said: “The water jetting industry today is completely different to when I started. The safety clothing and the equipment we use are so much better and we have more safety systems in place.
“You can’t compare now and then. It’s not that people didn’t want to work safe then. We just know a lot more now. Methods have improved and the WJA is there to set standards. It’s an industry I’m proud to be part of.”
WJA Director David Kennedy said: “Steven’s experience as a water jetter reflects the great strides made across our industry since the WJA was established.
“Our Codes of Practice – the Blue Code for high pressure and ultra high pressure water jetting and the Red Code for water jetting in the drainage industry – along with our training programmes, have had a profound impact.
“The positive effect of companies involved in the UK water jetting industry working together through the WJA to achieve common goals in terms of safety and service standards cannot be underestimated. Colleagues like Steven have benefited with long and rewarding careers.”
Steven had been working as a train driver at British Steel in Middlesbrough when he lost his job. He knew nothing about water jetting when he joined Walton Mole.
The company was run by Douglas Walton, son of its founder SR Walton, one of the pioneers of water jetting in the UK.
“The first thing I thought was, this looks dangerous,” he recalls. “I wasn’t allowed to hold a water jetting lance until I’d done six months on the pump and six months on the foot valve.
“Then I was trusted to go on the lance. I have WJA qualifications now, but I’m still learning. You have to respect the power of high pressure water, and every job is different. That’s why I love it.”
Over the years, Steven has had to demonstrate the power of water jets to emphasis the need for other workers to stay away.
“I was working in the steel works in a controlled space when a welder walked straight into it,” says Steven. “I told him he was putting himself in danger, but he wouldn’t believe me. So, I cut up a pallet with my lance and he was gobsmacked.”
He says the work was more physically draining in the early days, as their jetting systems, with high water flow rates and at pressures up to 15,000 pounds per square inch (PSI), created a high reaction force.
Modern systems are better engineered. They use finer jets, so flow rates are lower, but pressures are higher – up to 40,000 PSI. It is a set up that creates a lower, smoother, reaction force so is easier to handle.
“Water jetting is all about technique and technical knowledge. That’s the skill in the job and something that takes years to learn,” says Steven. “But it still pays to have a bit of muscle.”
In 40 years of water jetting, Steven has worked in all imaginable environments carrying out every imaginable water jetting task. His favourite was a hydrodemolition job he worked on in 1990.
Walton Mole was commissioned to cut through a 36-inch diameter concrete support column under the Thelwall Viaduct which takes the M6 over the Manchester Ship Canal.
The top of the leg had been chopped off with a hydraulic pecker. But the bottom of it needed to be cut with far more precision, because it would determine in which direction it would fall.
Steven says: “There was only one safe direction the column could go and hydrodemolition was the best way to guarantee that would happen. We were cutting at 15,000 PSI using 50 gallons of water a minute, and it took us 33 hours to get through it.”
The water jetting team used a mini digger fitted with a hydrodemolition attachment to carry out most of the cutting. The final cuts were made with handheld lances with gimbals operating at 15,000 PSI and 10 GPM.
Once the water jetting had been completed, with a little nudge from the pecker, the column toppled to exactly where it was supposed to.
Steven is employed by WJA member ASL Powerstream Services as a site supervisor. He works alongside Richard Walton, Douglas Walton’s son and now ASL PowerStream’s Engineering Director, both having worked together for many years at Walton Mole.
Steven’s son, James, aged 29, also works for ASL Powerstream as a water jetter. Though he is planning a long-term career as a psychological counsellor.
So, would Steven recommend a career in water jetting now? “Of course, I would,” he says. “It’s technically very interesting. The money is good and it’s very rewarding. As long as you respect the power of water.”