Member Case Studies

Jetting robot joins demolition fast lane
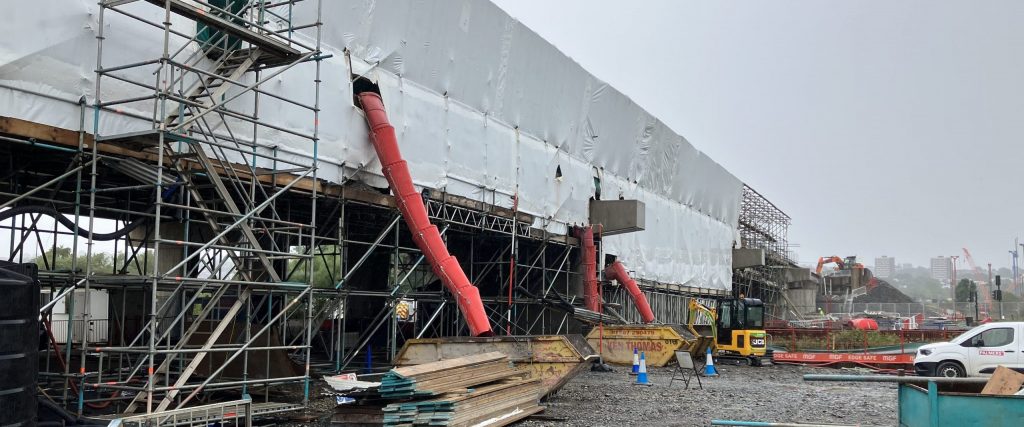
A hydrodemolition project to remove concrete from a carriageway has contributed to a major improvement scheme bringing much-needed additional capacity to an important road transport corridor for the North East of England.
Under the watchful eye of the Angel of the North, a robotic water jetting machine has been used to remove concrete from one of the carriageways of the A1, a strategic inter-regional route for commuting, freight and leisure.
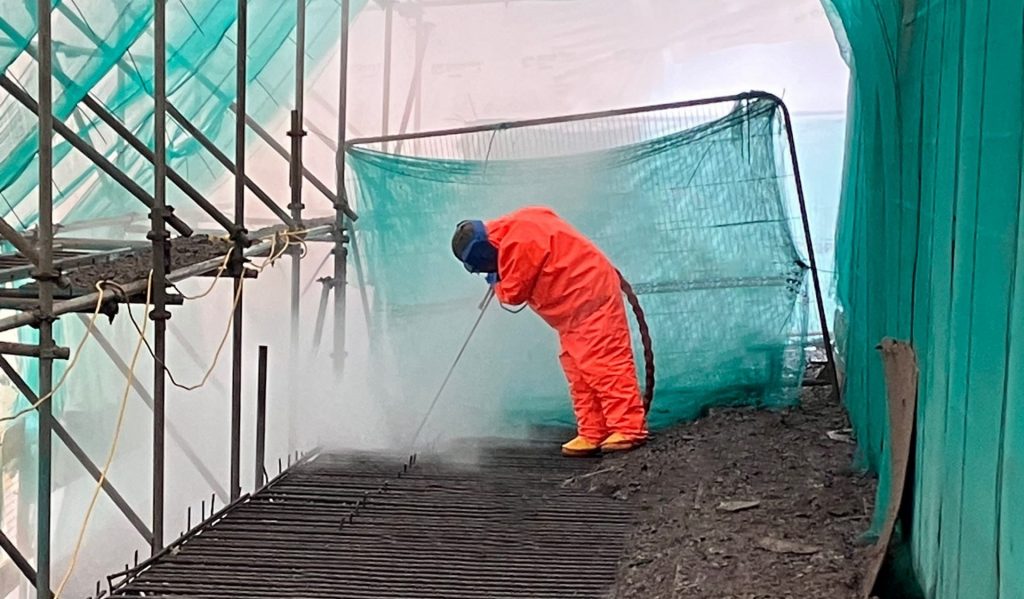
The ultra-high pressure water jetting technique was selected as the safest and most effective way to remove the concrete while retaining the rebar needed to allow the carriageway to be widened.
The work has been completed in support of a programme led by National Highways delivery partner Costain to improve a four-mile stretch of the A1 from Birtley to Coal House in Tyne and Wear.
The principal contractor for the hydro-demolition project was Aquaforce Concrete Services, a member of the Water Jetting Association (WJA).
The company, part of civil and structural engineering specialist Freyssinet UK, was responsible for the scaffolding, access and encapsulation design and installation, as well as all demolition duties.
Hydro-demolition advantages
Work began on the 13-week project in July 2022. Aquaforce had the task of removing concrete on the northbound carriageway at the Kingsway (Coal House) roundabout, where two lanes in both directions were to be widened to three.
The project had two key elements – removal of concrete from a 1.2m strip of the carriageway running for 146m across the Kingsway interchange, and the removal of a 750 × 750mm concrete outer parapet.
This would expose a 1.9m strip of reinforcing bar onto which Costain could attach new reinforcement for the third carriageway, which would sit on new concrete pillars and steel beams.
Costain had selected hydro-demolition as the primary method to carry out the demolition because of its recognised advantages for safeguarding rebar that needed to be retained.
Hydro-demolition uses high-and ultra-high-pressure water jets to blast concrete off the reinforcement. It works by the water jets exploiting tiny cracks and fissures in the concrete and exploding it. The steel reinforcement does not have the same structural weaknesses, so remains unaffected, left clean and ready for concreting.
Most sustainable option
The alternative method, using pneumatic or hydraulic mechanical breakers, takes up to five times longer and greatly increased the risk of reinforcement being damaged. In the case of handheld tools, it also has significant health and safety disadvantages.
Lee Miller, Aquaforce project manager, explains, “Mechanical tools would damage the rebar system resulting in more work to repair, strengthen or even replace it, adding to costs and project timescales.
“With handheld systems, like jackhammers, they also significantly increase the risk of hand-arm vibration injury. These issues make water jetting the faster and more sustainable demolition method.”
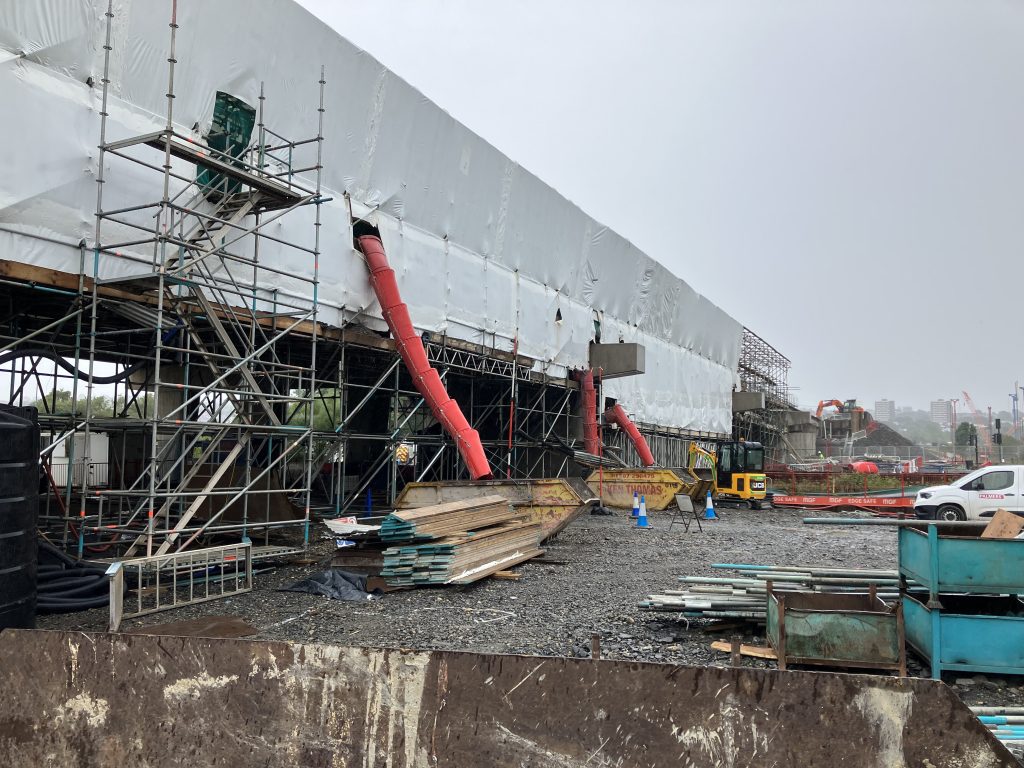
The Swedish Concrete Research Institute has also found a repair carried out using hydro-demolition had a life expectancy of 21 to 35 years compared with seven to 12 years if mechanical tools are used.
These advantages, when combined, strongly indicate that hydro-demolition also delivers outcomes with a lower carbon footprint than conventional mechanical methodologies.
Safe and productive hydro-demolition
The Water Jetting Association is the member body for the water-jetting industry. It represents contractors, manufacturers, hirers, training providers and water-jetting users.
The WJA has two internationally recognised codes of practice – the Blue Code for use of high-pressure and ultra-high-pressure water jetting and the Red Code, for the use of water jetting in drains and sewers and surface preparation up to 275 bar.
The WJA is also the UK’s largest water-jetting training provider. Its City & Guilds-accredited courses are delivered by registered training providers and approved instructors.
Robotic water jetting
With preparatory works completed, the Aquaforce teams could begin the hydro-demolition project in earnest, with work carried out over a series of day and night shifts.
Concrete had to be removed from six deck spans. The deck was 220mm thick. An estimated 18m3 of concrete had to be removed from each span, making the total volume of concrete to be removed 107.5m3.
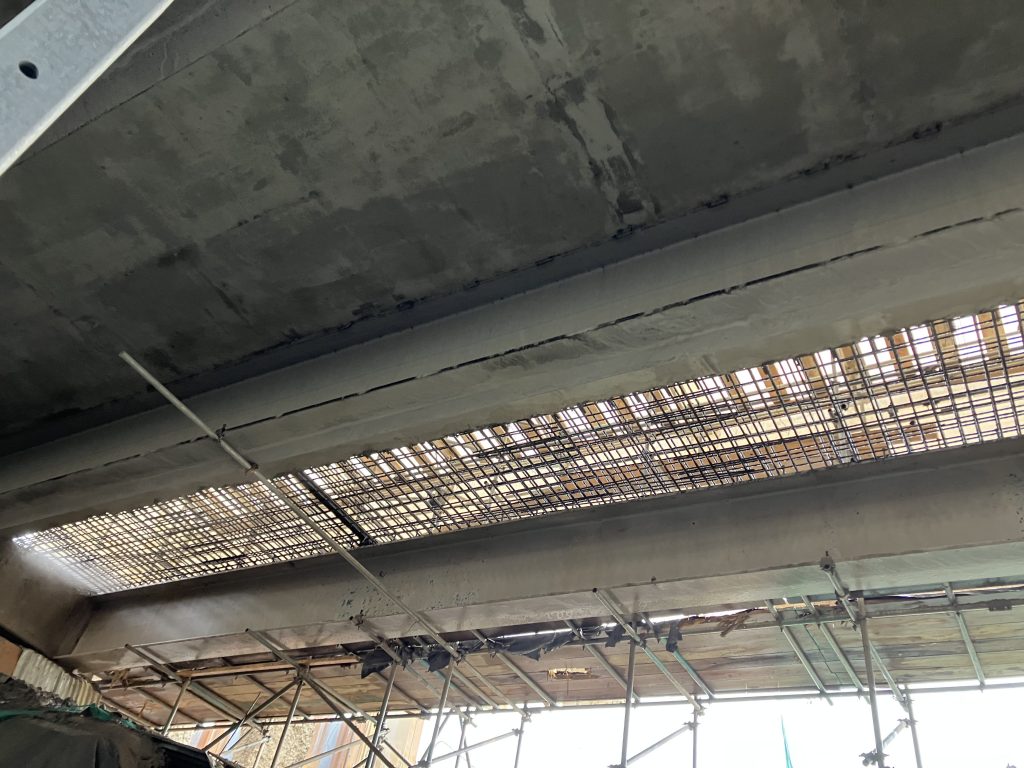
Aquaforce used two hydro-demolition methods – semi-automated water jetting using a robotic machine and hand-lance water jetting. For part of the process, it also used a mechanical breaker.
Concrete in the 1.2m strip of deck was removed with a Conjet 557 XL hydro-demolition robot, supplied by hire specialist Doornbos, also a WJA member.
It was the fastest methodology for removing material from such a large, uniform area. It also minimised the risk to the water jetting operative, who could stand away from the jetting heads.
The hydro-demolition teams also used hand lance water jetting to remove concrete from hard-to-reach areas, where necessary. As the parapet, including associated reinforcement, was not being kept, Aquaforce used an excavator with a mechanical breaker to reduce it to within 100mm of the base.
The final 100mm of concrete was then remove with hand-held water jetting lances, and the unwanted rebar cut free with diamond saws. This was the fastest and safest methodology, given that the reinforcement did not need to be preserved and the amount of hand lance jetting work needed was reduced.
Flexible operation
The hydro-demolition robot was operated at a pressure of 1100 bar (16,000psi), with a flow rate of 256 litres per minute. The hand lance water jetting was carried out at the same pressure with a flow rate of 80 litres per minute.
Potable water needed for jetting was piped from a mains hydrant 63m from the worksite, with around 200,000 litres of water used every day.
Concrete removal on each span was completed in around ten days. The hydro-demolition teams moved forward three metres per day, removing around 4.8 tonnes, or 2m3, of concrete.
The process was accelerated with additional night shifts while working directly above the roundabout to limit the time roads had to be under traffic management.
Where rebar needs to be conserved, hydro-demolition is five times faster than mechanical concrete removal, so it shortened the period of traffic management, minimising disruption for road-users.
Wastewater filtration
The encapsulation sheeting contained the tens of thousands of shards of concrete blasted from the structure by the water jets each day – as well as noise generated by the water jets.
A secondary deck was built below the hydro-demolition work teams to capture these concrete shards and the jetting water.
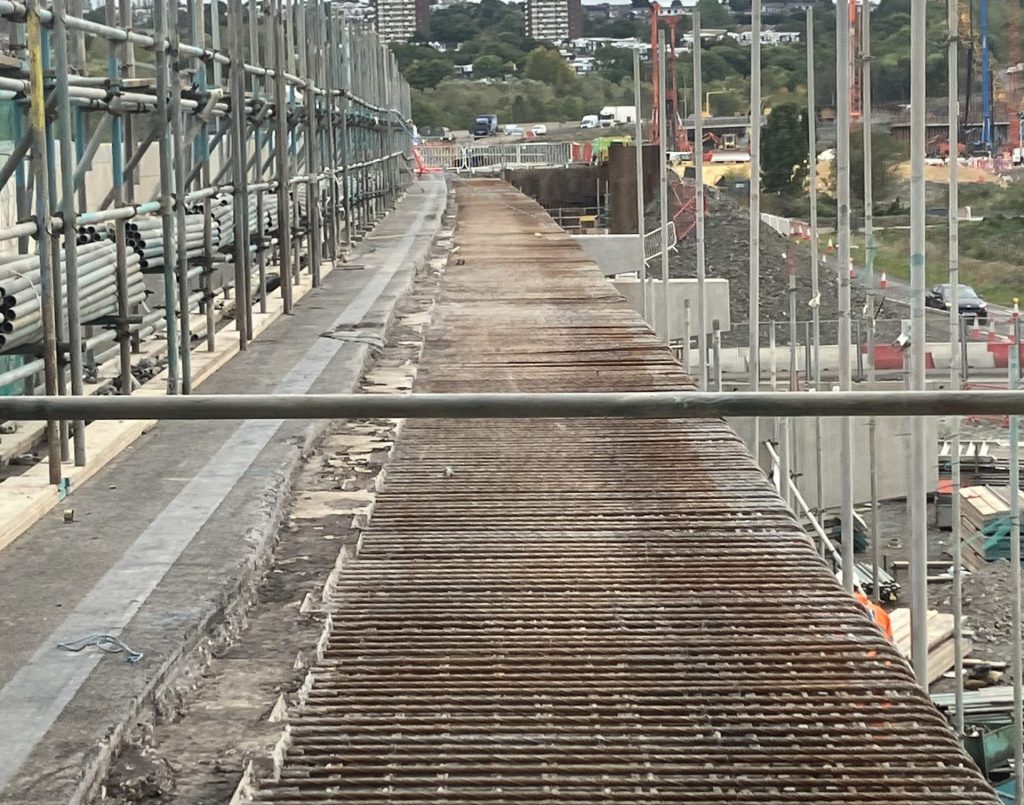
This is where hydro-demolition provides another key advantage, especially when working on a busy highway: dust pollution is minimised because the concrete particles remain suspended in water.
Steel sheeting was used to protect elements of the bridge structure from flying debris. The concrete debris was chuted into skips and taken away to be recycled.
Water was also captured and piped for 60m to mobile filtration units where silts were separated and the water was treated to give it a neutral
pH. This allowed it to be disposed of, with permission from Northumbrian Water, in a main sewer.
Valuable contribution
Aquaforce completed the hydro-demolition project on time and on budget at the end of September 2022, removing 256 tonnes of concrete in total.
WJA President John Jones said: “This project demonstrates the valuable contribution of hydro-demolition when modifying concrete structures during highway improvement programmes.
“Depending on work required and site conditions, hydro-demolition teams can be mobilised quickly and flexibly to complete urgent tasks, or be integrated into wider work programmes.
“A key concern, always, is the need to maintain a safe working area, given the unique risks associated with high- and ultra-high water jetting. This needs effect and strictly applied safe systems of work, including clear communication with other site personnel.”
Find out more
Talk to the WJA about the water jetting advantage: +44 (0) 20 8320 1090 info@waterjetting.org.uk.